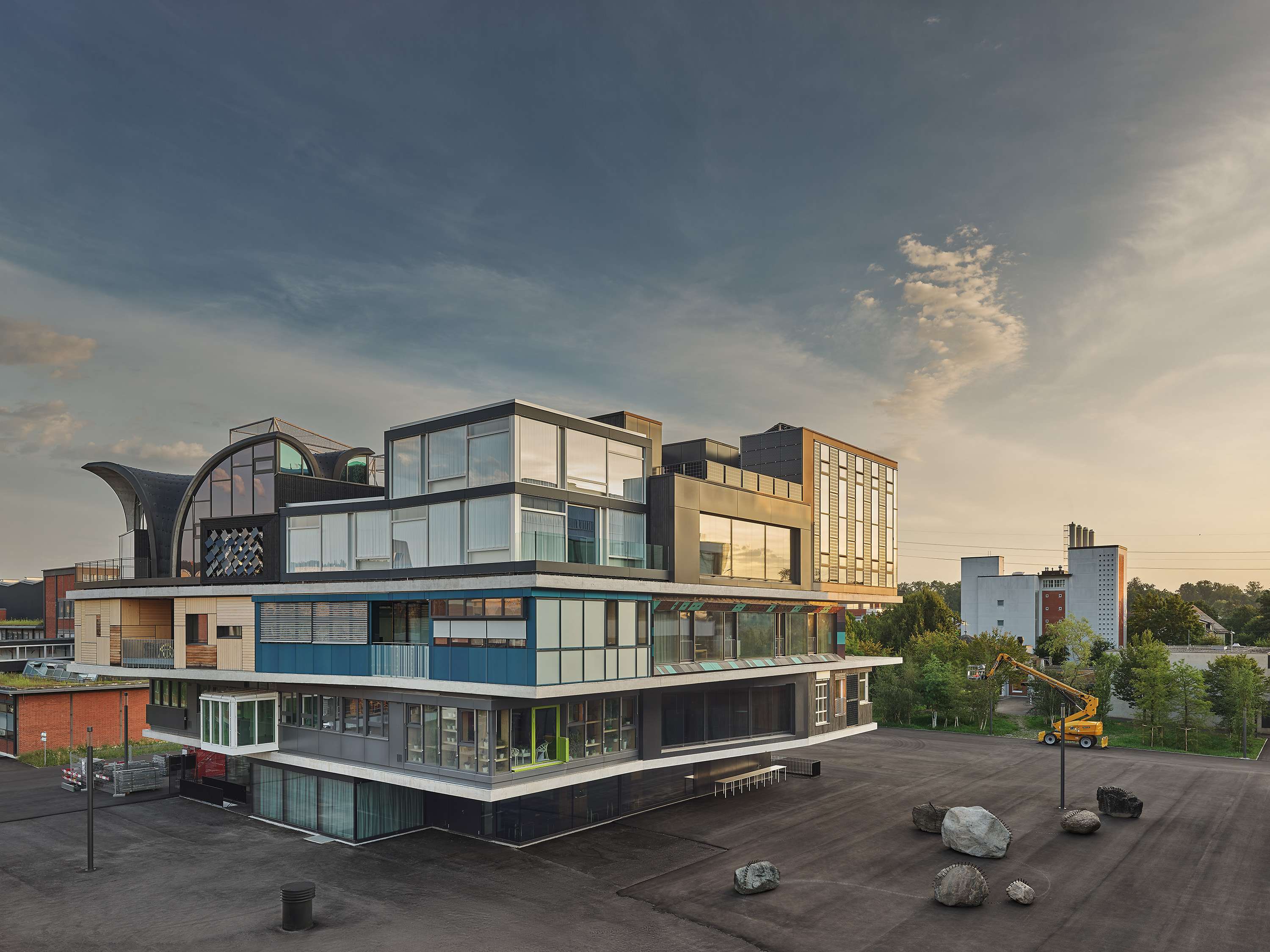
STEP2
Building Innovation at Nest
STEP2 is an innovation and research unit at the NEST platform. It combines latest research in energy simulation, digital fabrication and upcycling of materials. The unique innovations demonstrated here for the first time are: A structurally and material optimized, multi performance concrete ceiling, which integrates acoustic absorption, diffusion and a thermal buffer. A helical stair that showcases a dramatic reduction of concrete use thanks to high-performance materials. Interior cladding, made from upcycling of fibrous waste using a novel water-based binder. A closed-cavity-façade with natural ventilation of the cavity. All innovations in STEP2 are developed by industry partners and are market ready with the goal to provide a positive sustainability impact on a larger scale.
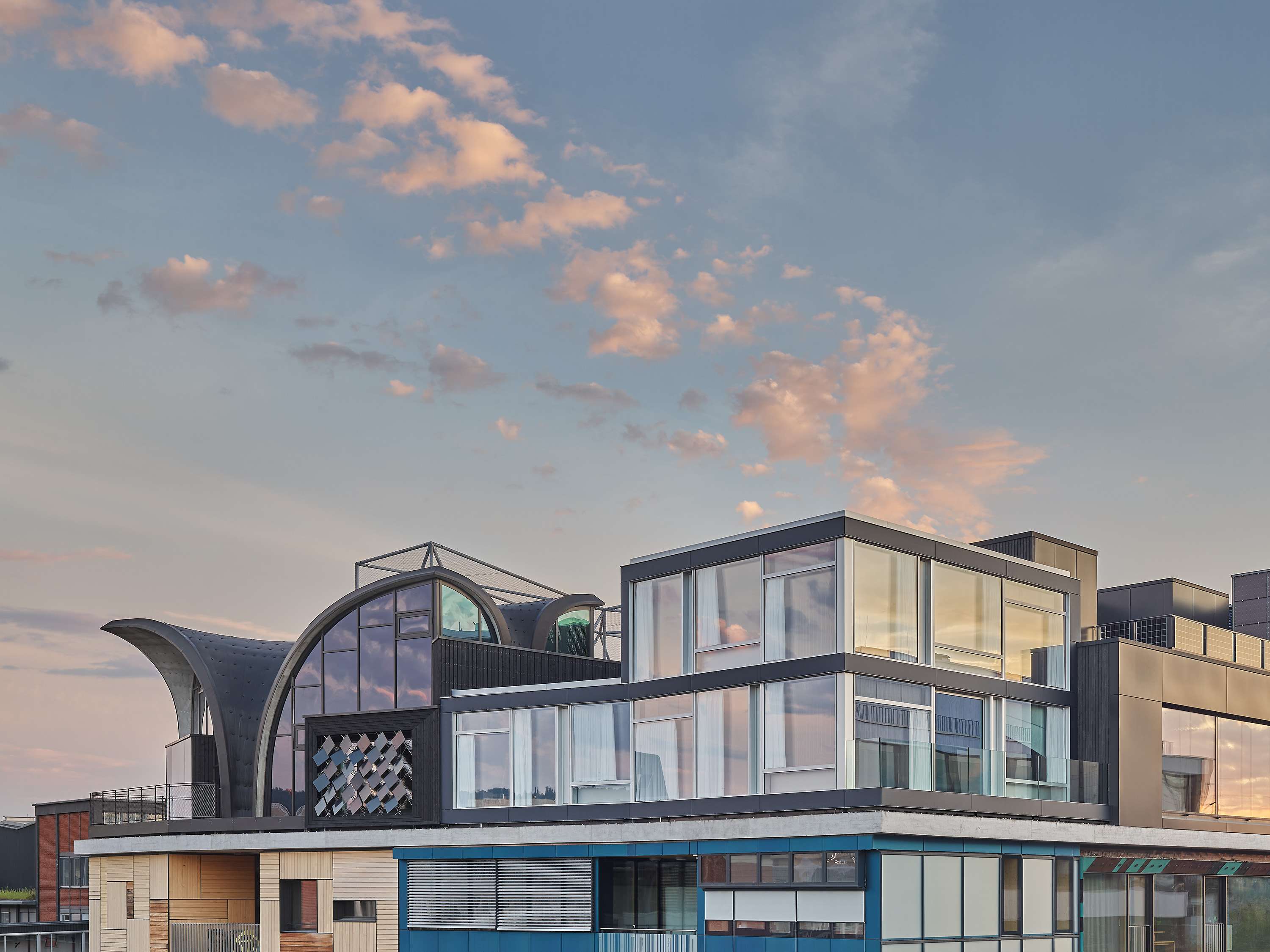
Energy Concept
The project started with comprehensive studies of the location, the environment, the intended use and the local climate. Using thermodynamic simulations, control strategies for an adaptive building envelope were developed. The energy concept uses only passive systems such as natural ventilation and lighting as well as passive heating and cooling.
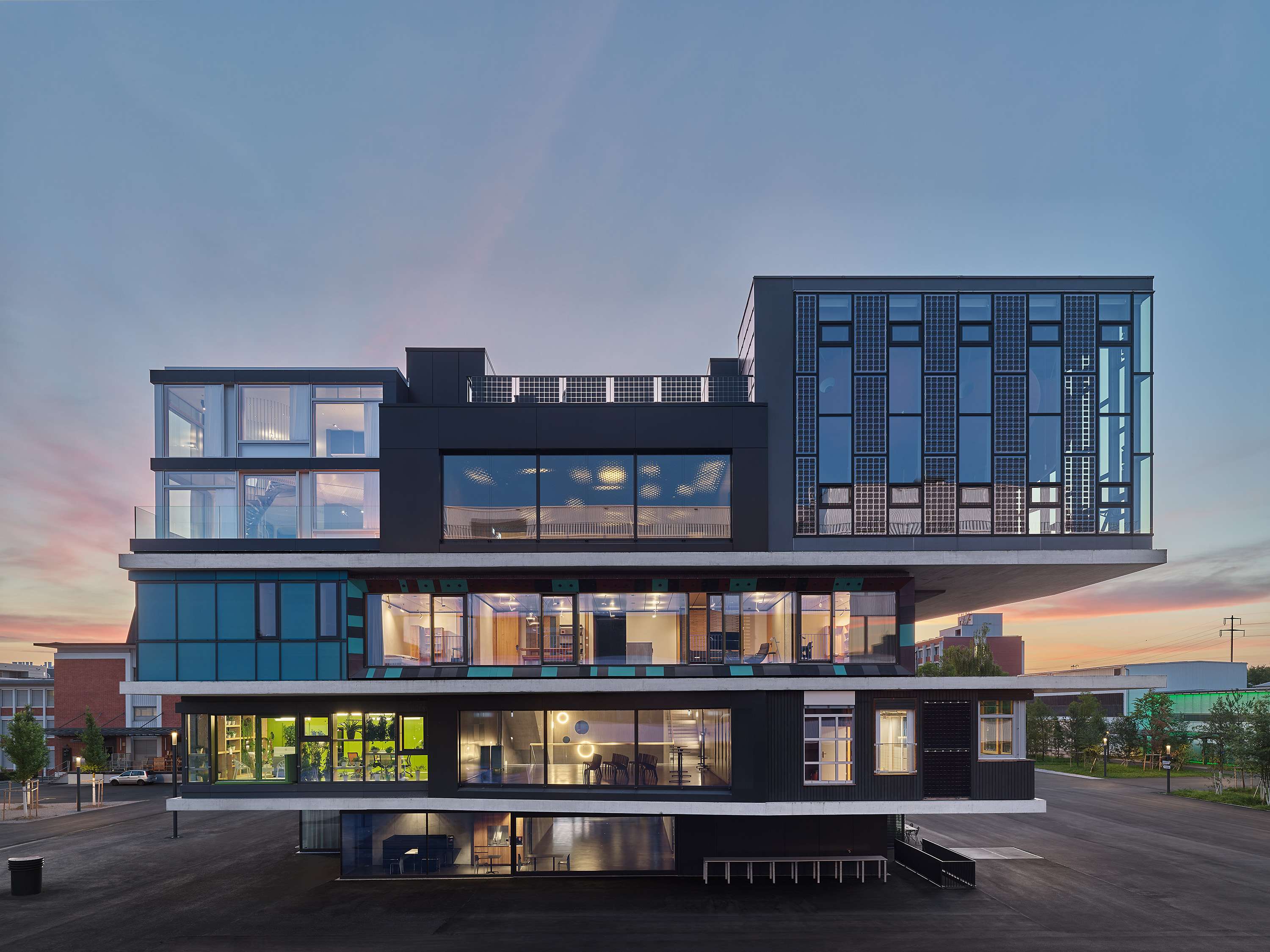
Integral design approach
The following building elements are an integral part of the energy concept: High thermal glazing with high spectral selectivity. Controlled, natural ventilation by using automated ventilation flaps. Adaptive sun protection systems. An exposed concrete ceiling that is activated to buffer thermal energy. Energy specialist: WaltGalmarini
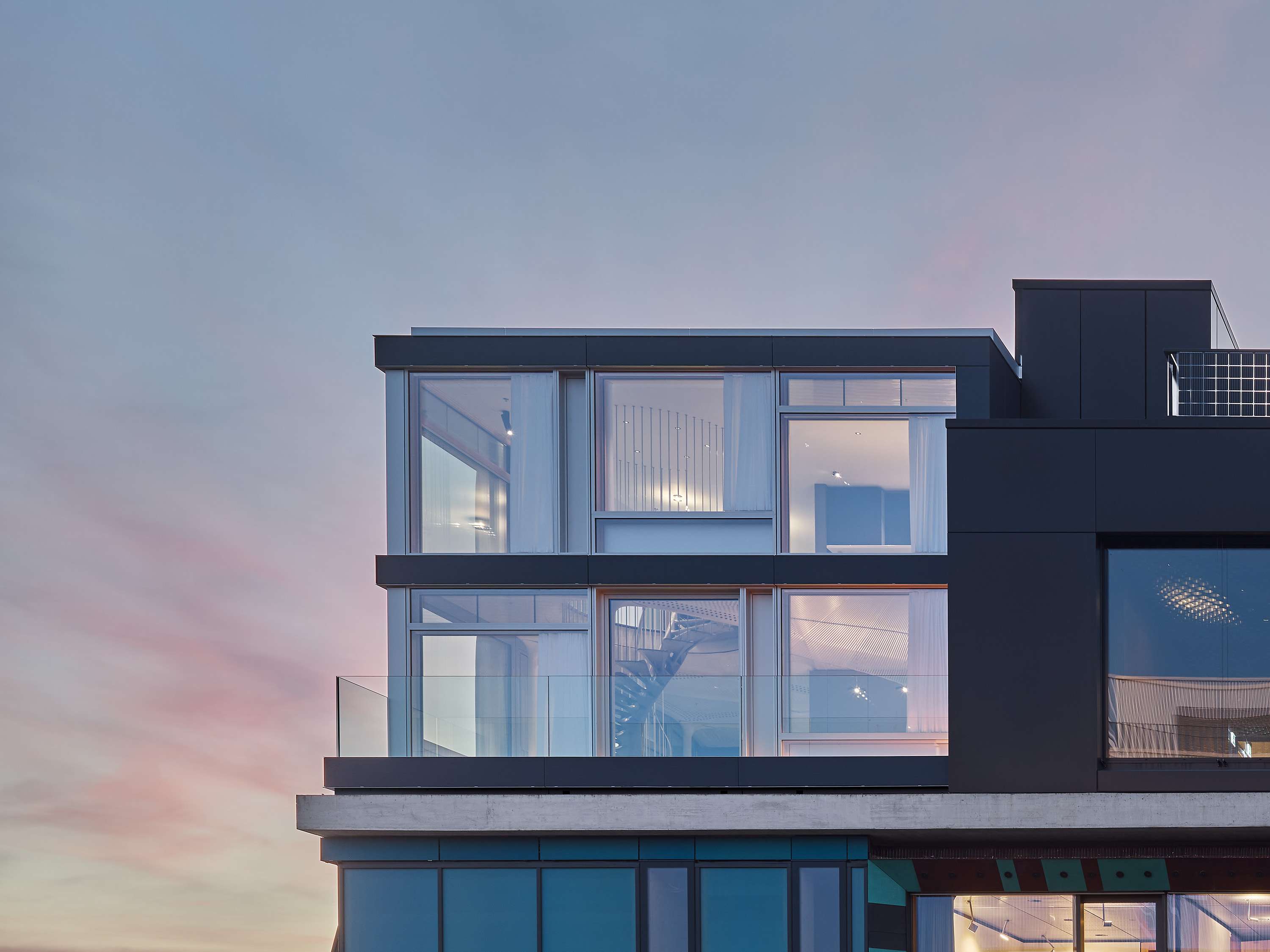
Integrated Performance Floor
The structurally and materially optimized, multi performance concrete floor saves 45% CO2-eq in comparison to a solid concrete slab at a span of 5 meters. The floor can serve spans up to 14 meters, where the CO2-eq savings increase to 65%. The reduction in CO2-eq is achieved through a combination of geometric volume reduction, pre-tensioning and CO2 reduced concrete.
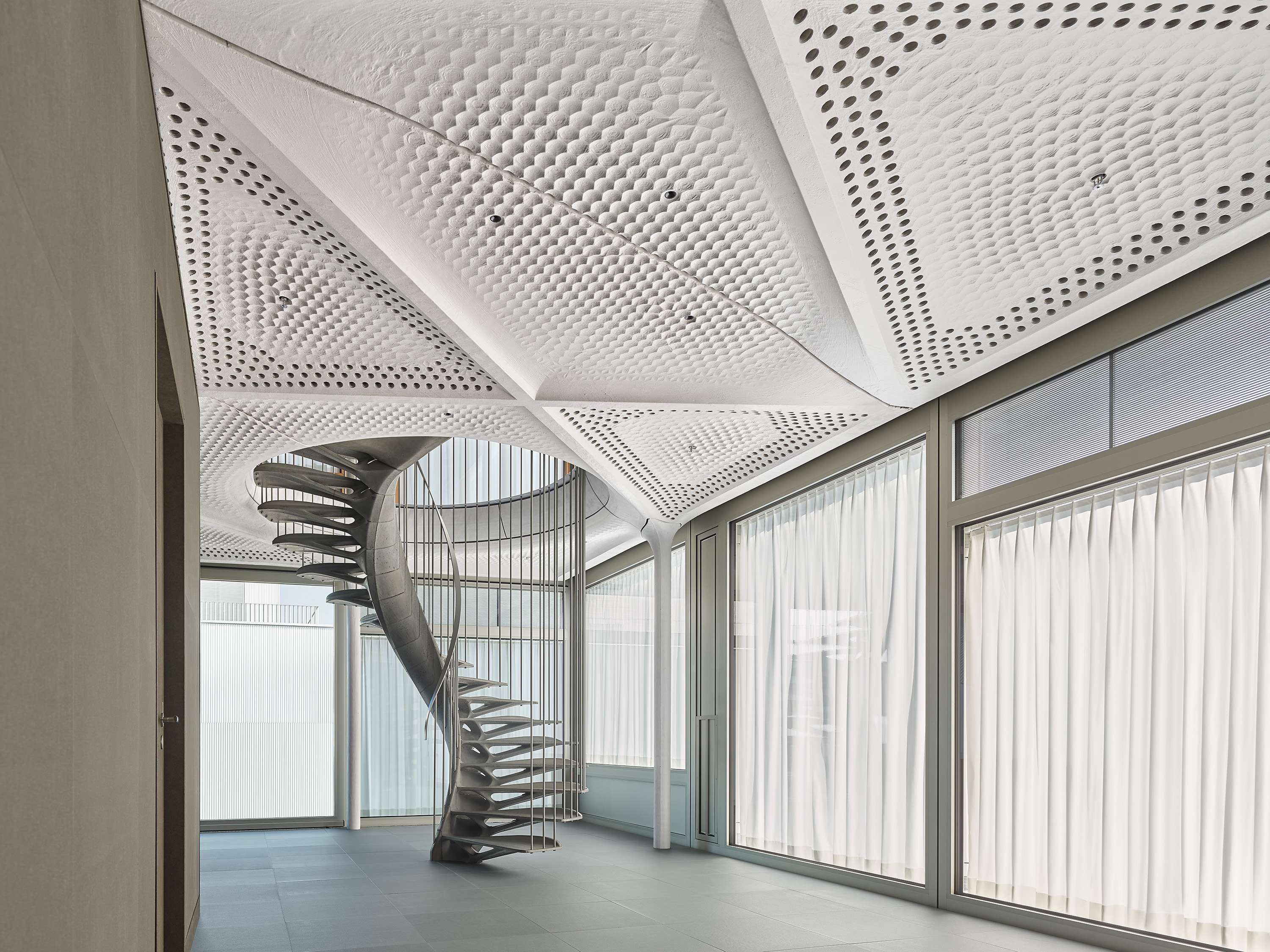
Energy saving synergies
The Integrated Performance Floor contains acoustic cavities that are filled with clay based acoustic foam. This allows for raw a concrete surface, which is essential to use concrete as a thermal buffer for natural ventilation. Furthermore, the underside of the floor is covered with a 3-dimensional pattern that increases the surface area by 15%, further enhancing the heat exchange between air and concrete. The floor is fabricated using large scale 3D-printing of re-usable formwork. The printer is a unique development with a print bed of 6 by 9 meters. Custom computational design and fabrication tools: ROK Architects | Structural design: WaltGalmarini Ingenieure | 3D-printer development and fabrication: Stahlton Bauteile AG | Clay foam innovation: BASF SE.
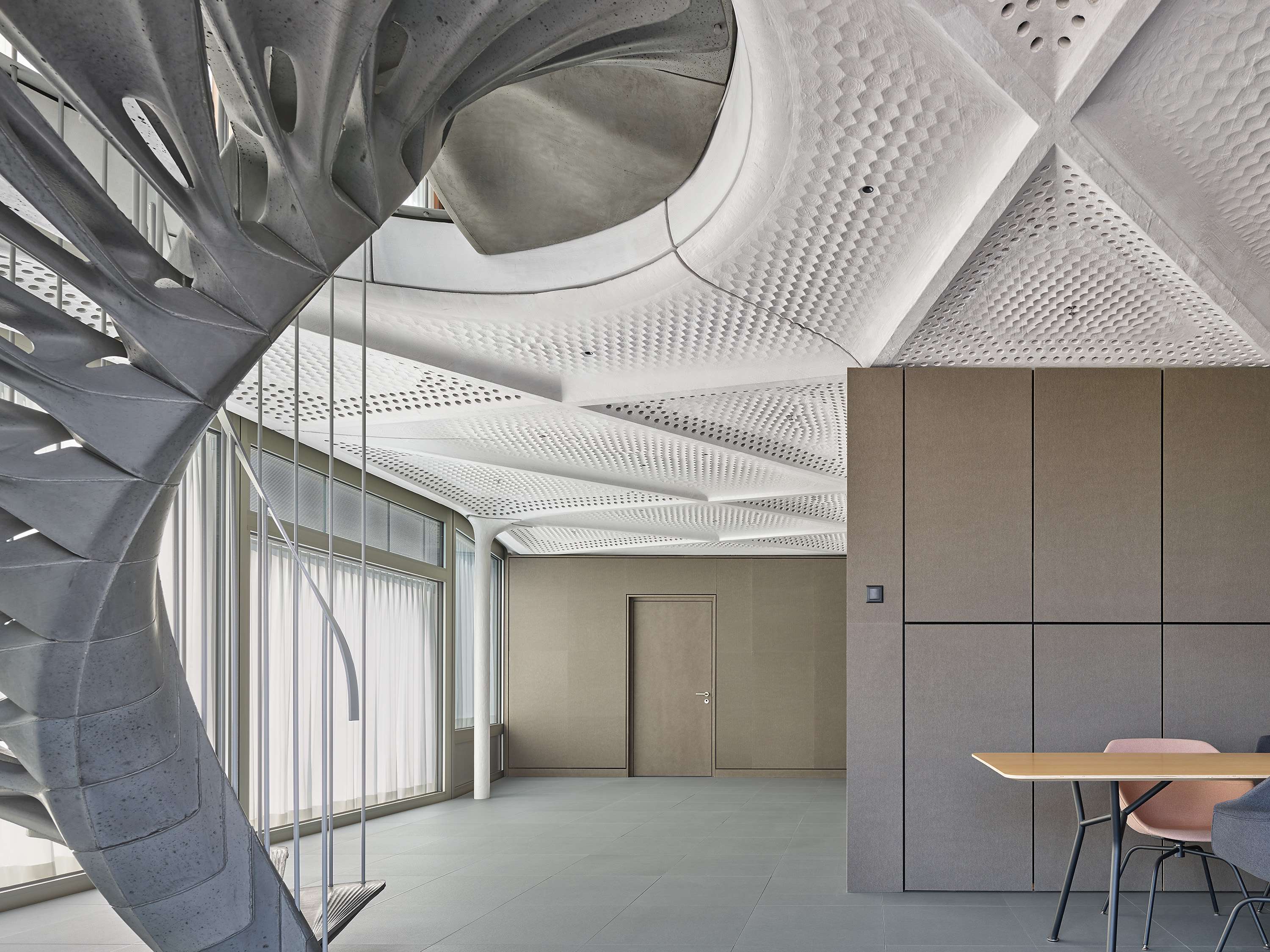
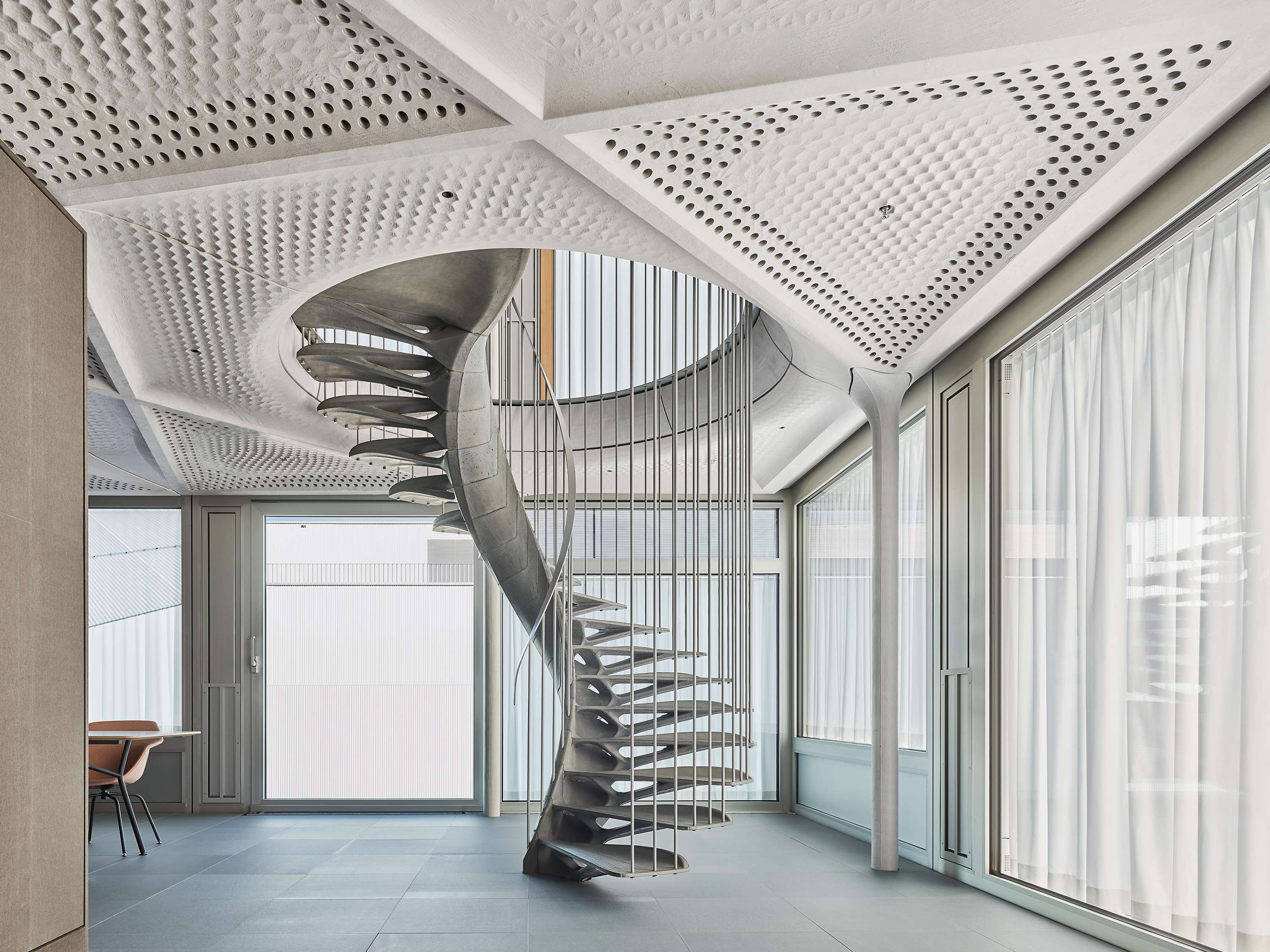
Cadenza
The stair designed in collaboration with dbt - ETH Zurich showcases circular economy in architecture with high-performance materials. Additionally, it demonstrates a structurally optimized use of material, with steps less than 20 mm thick and weighing only 45 kg. The efficiency is further enhanced by the concentration of reinforcement in three memory-steel post-tensioning bars located in the load-bearing stringer.
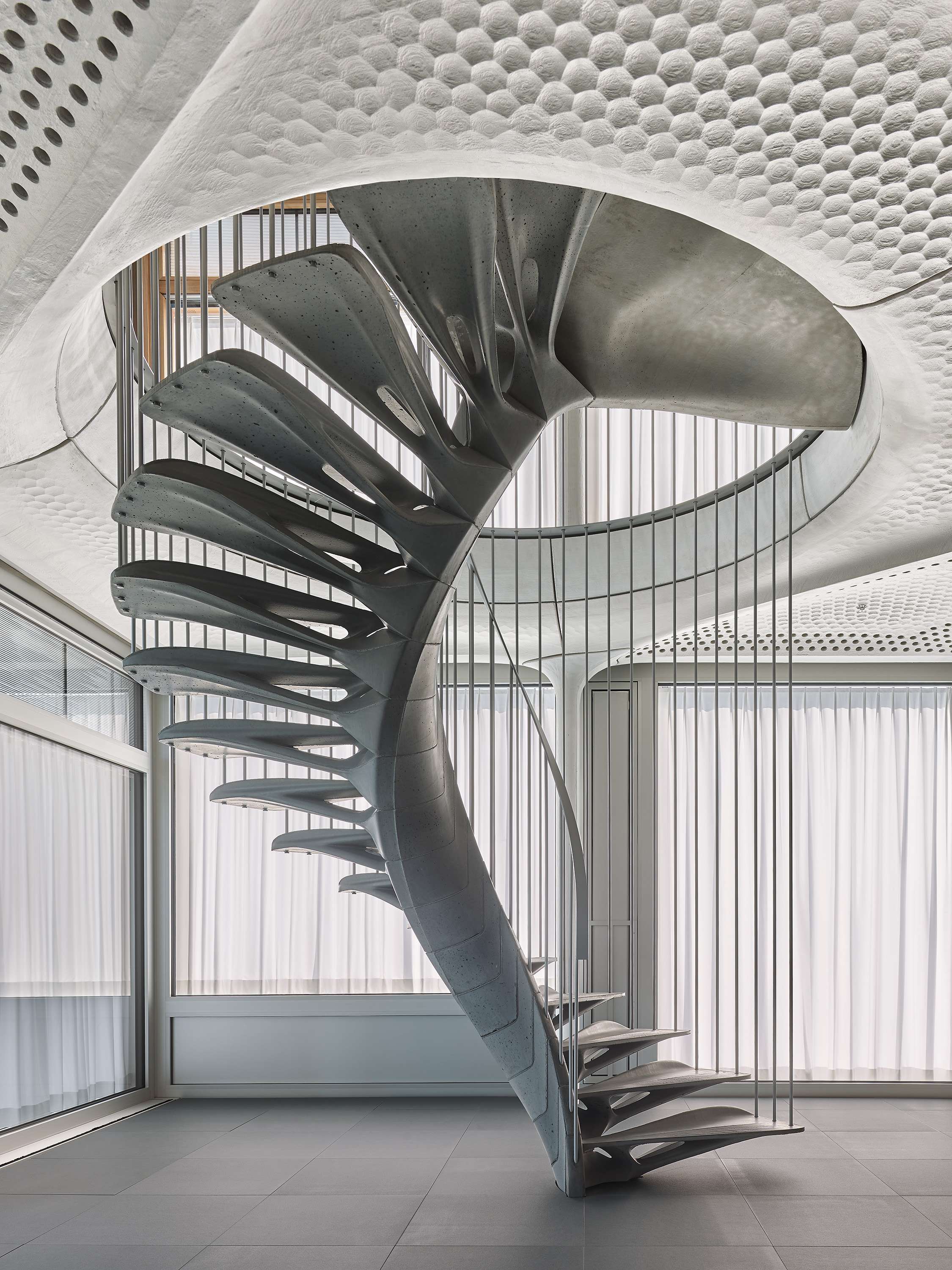
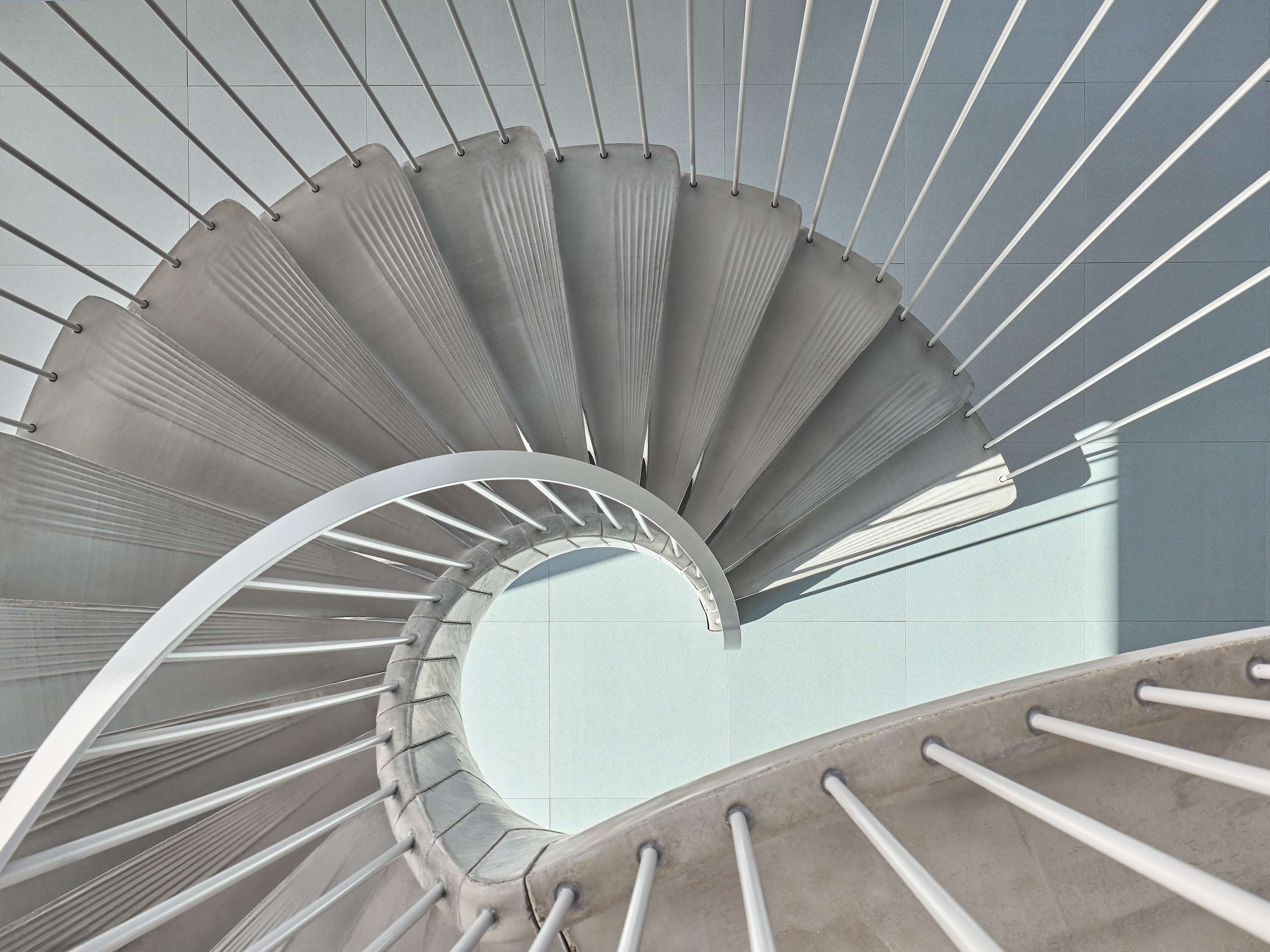
Design for disassembly
The complex geometry of the 16 concrete steps was achieved using a single set of reusable 3D-printed formworks. The steps and the landing were designed to be assembled with dry connections only, making the tectonic concept compatible with refurbishments and circular economy architecture, being modular, and ready to be dismantled and reassembled. Stair design: Digital Building Technologies - ETH Zurich, ROK Architects | Fabrication System: Digital Building Technologies - ETH Zurich, SW Umwelttechnik | Formwork Development and 3D Printing: Digital Building Technologies - ETH Zurich, Forward AM Technologies, New Digital Craft | Structural Design: WaltGalmarini | Precast Concrete: SW Umwelttechnik | Post-tensioning System: re-fer.
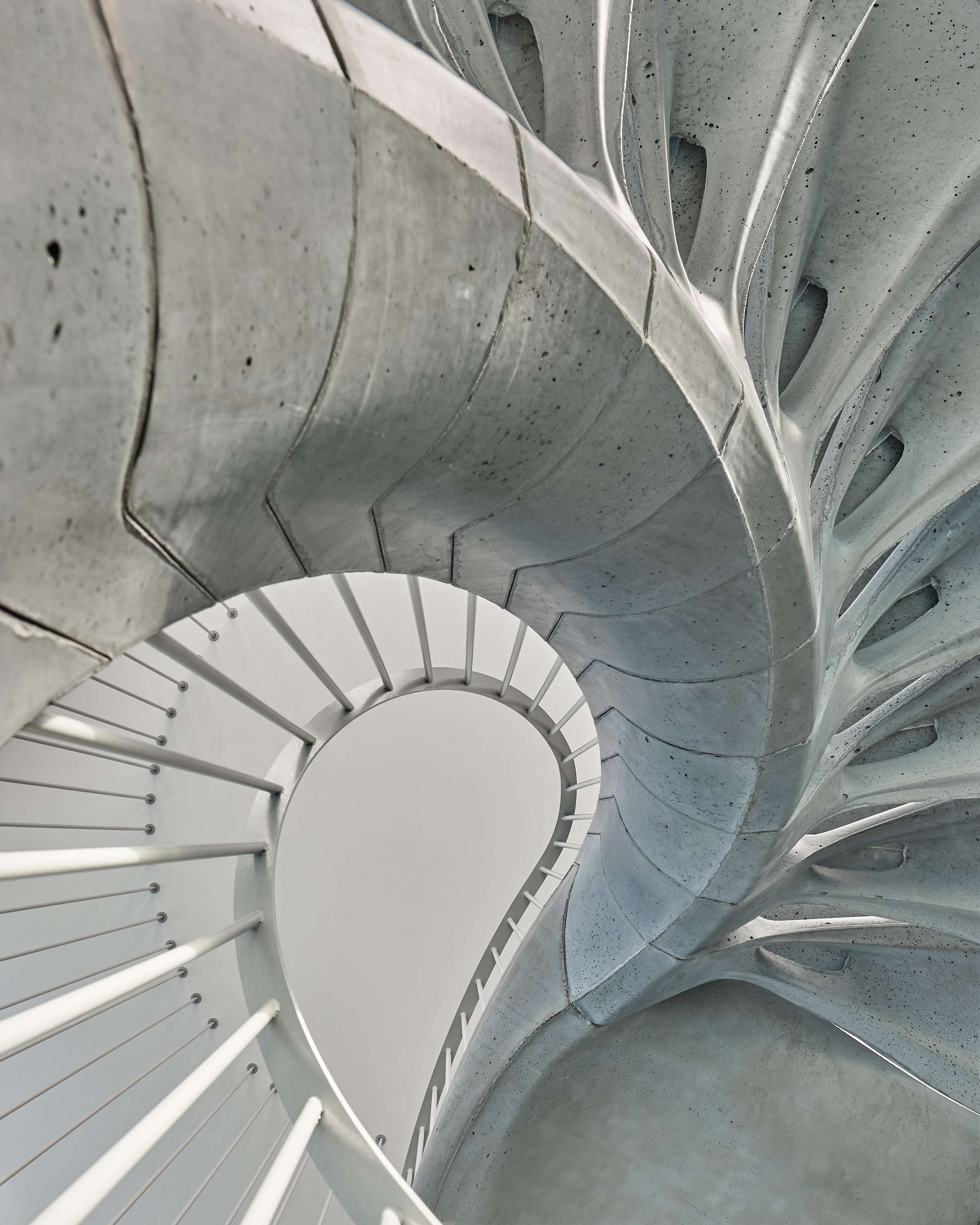
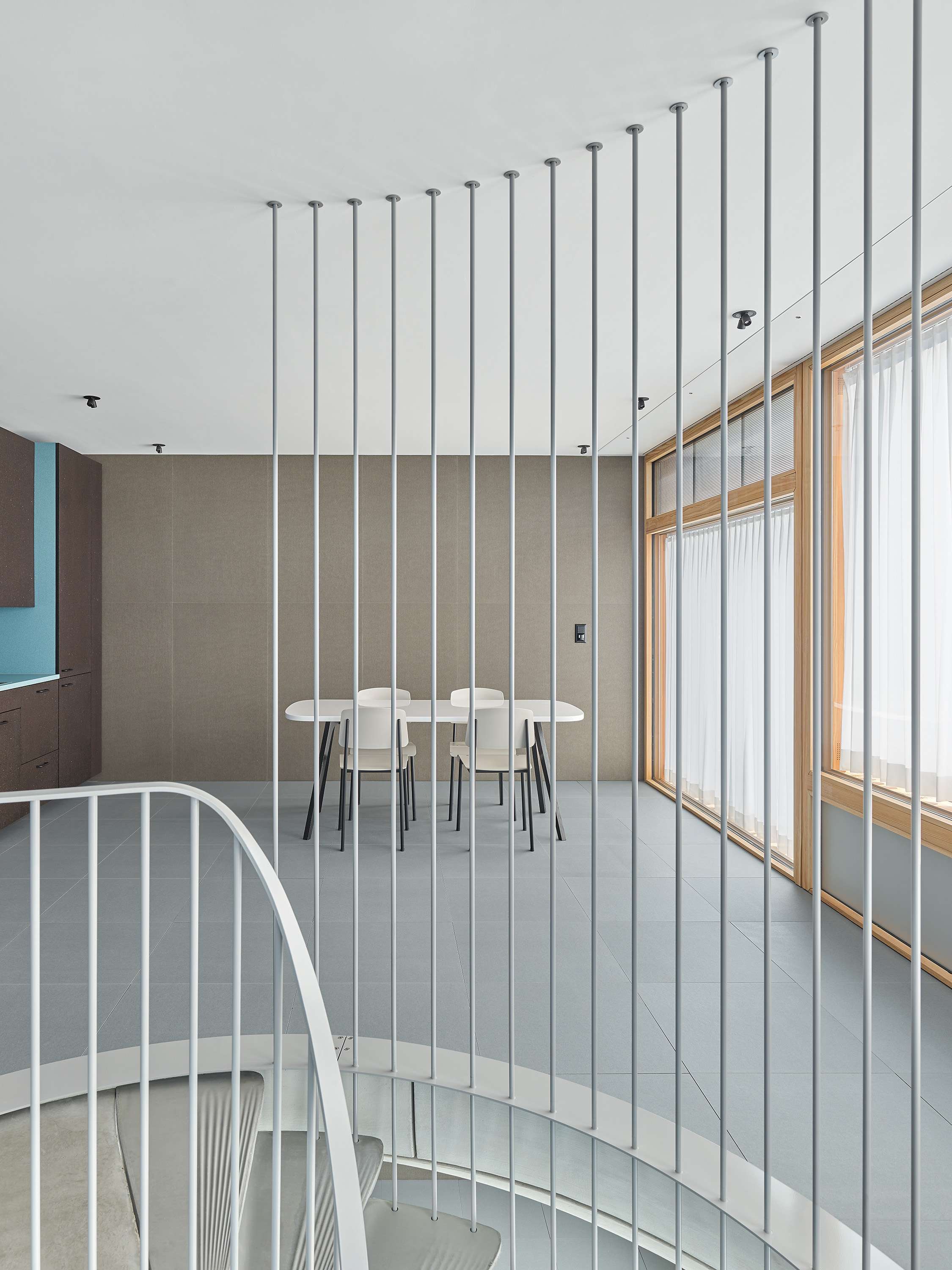
Upcycling Materials
Upcycling from waste materials is at the center of STEP2’s interior. High-performance flooring made from textile waste is used for the hollow floor construction. Panels made from paper cup waste cover the walls. All waste materials used are readily available in large waste streams. Central to the upcycling of those materials is BASF's innovative water-based binder which is low in gray energy and tolerant to waste material impurities.
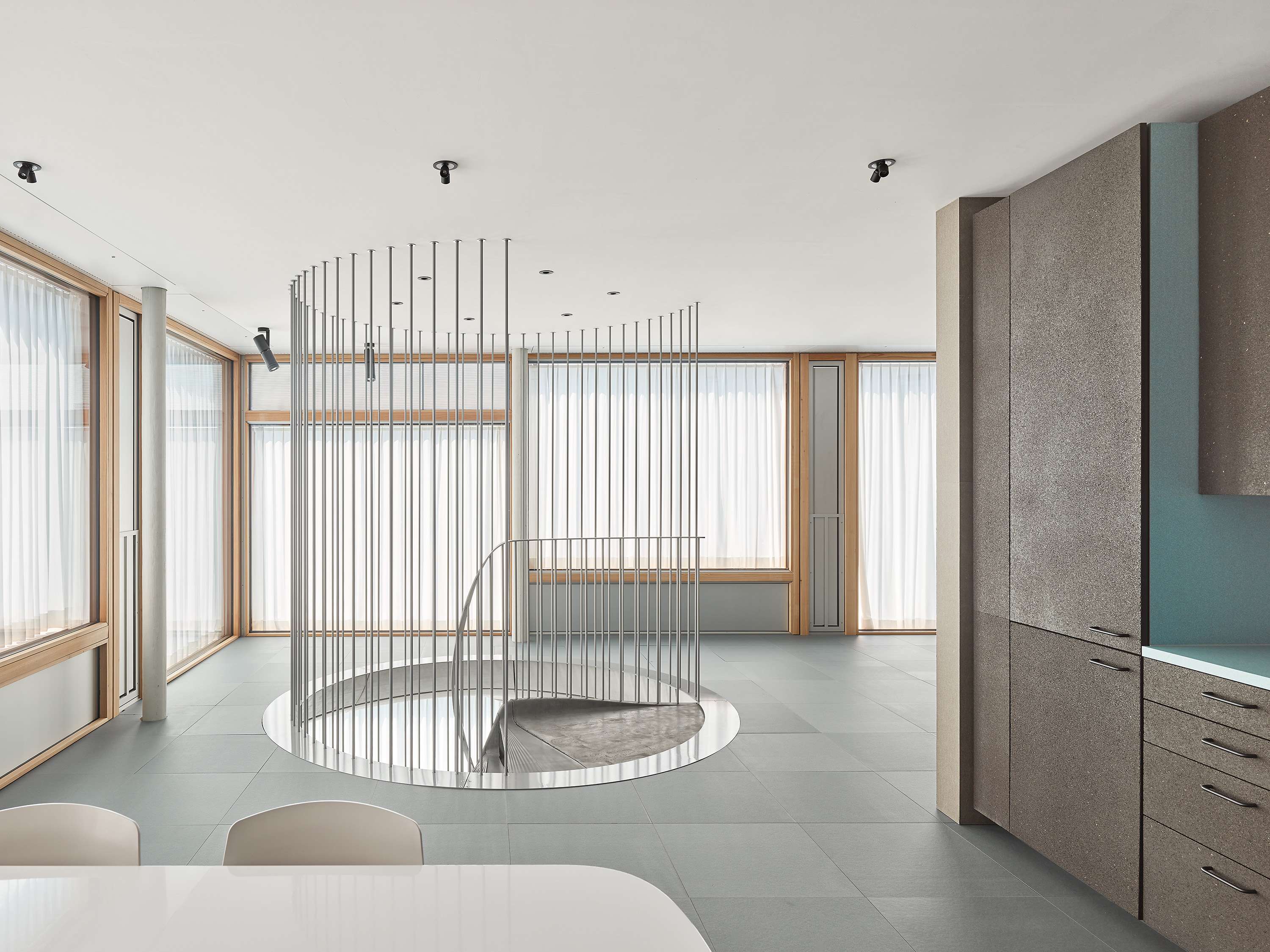
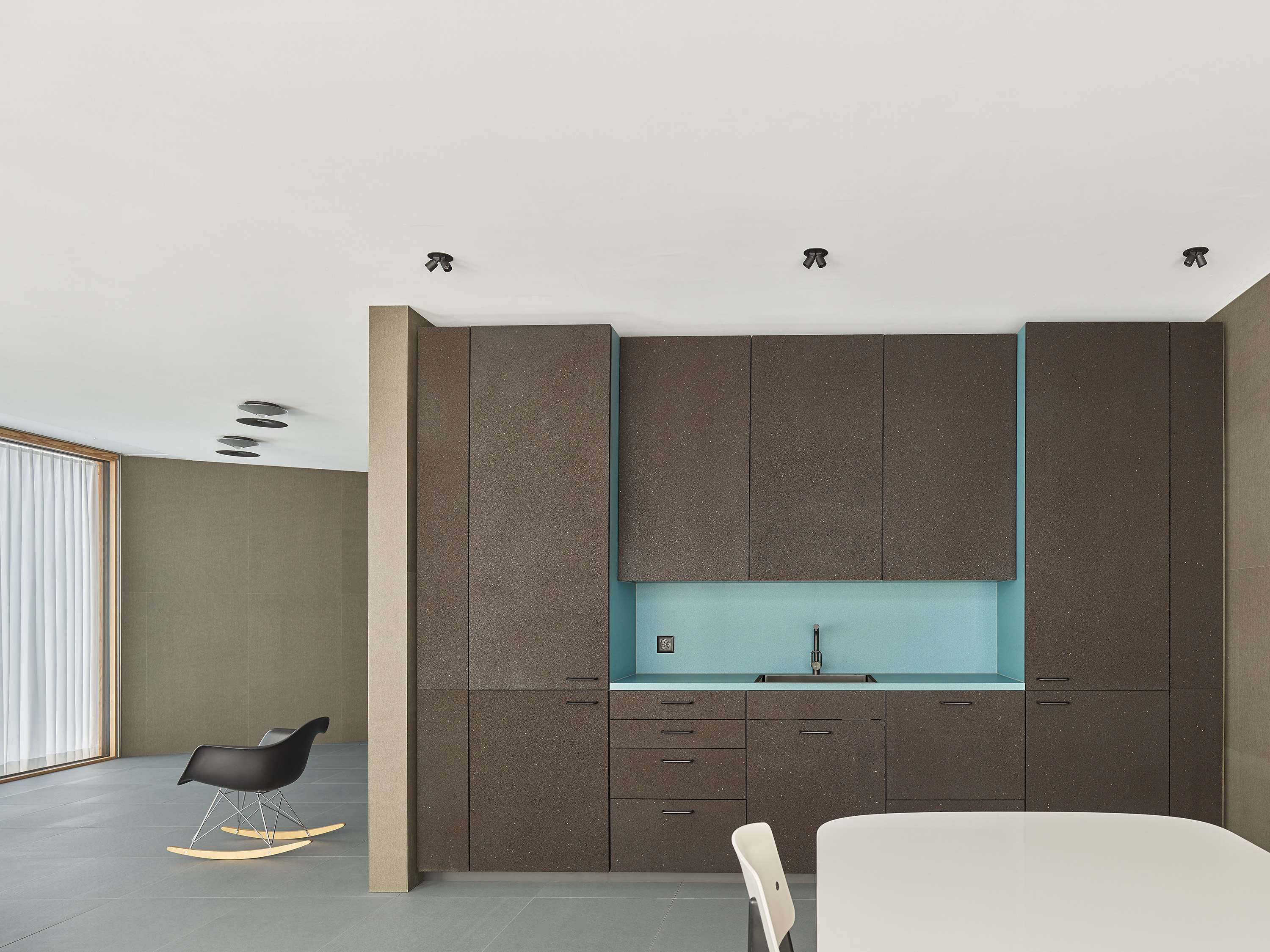
Market Ready and Impactful
The kitchen top and backsplash are covered in large scale tiles made from ocean plastic recovered from the Baltic Sea. The cupboard fronts are made from compressed industrial coffee grounds. Following the idea impactful innovation, all upcycling materials are already in the market or will be shortly. Partners and brands: BASF, Acronal, acForm, Coldharbour Tiles.
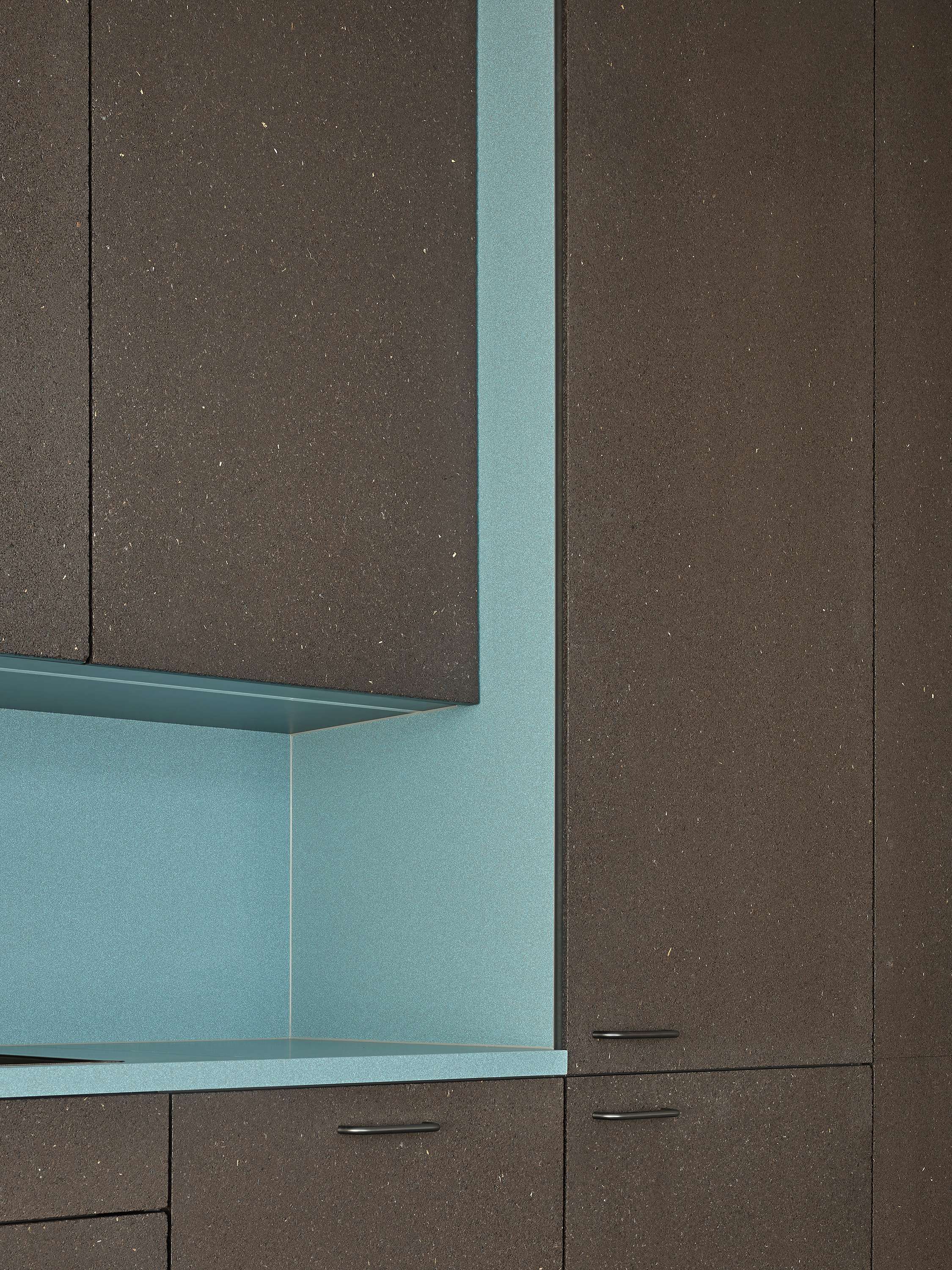
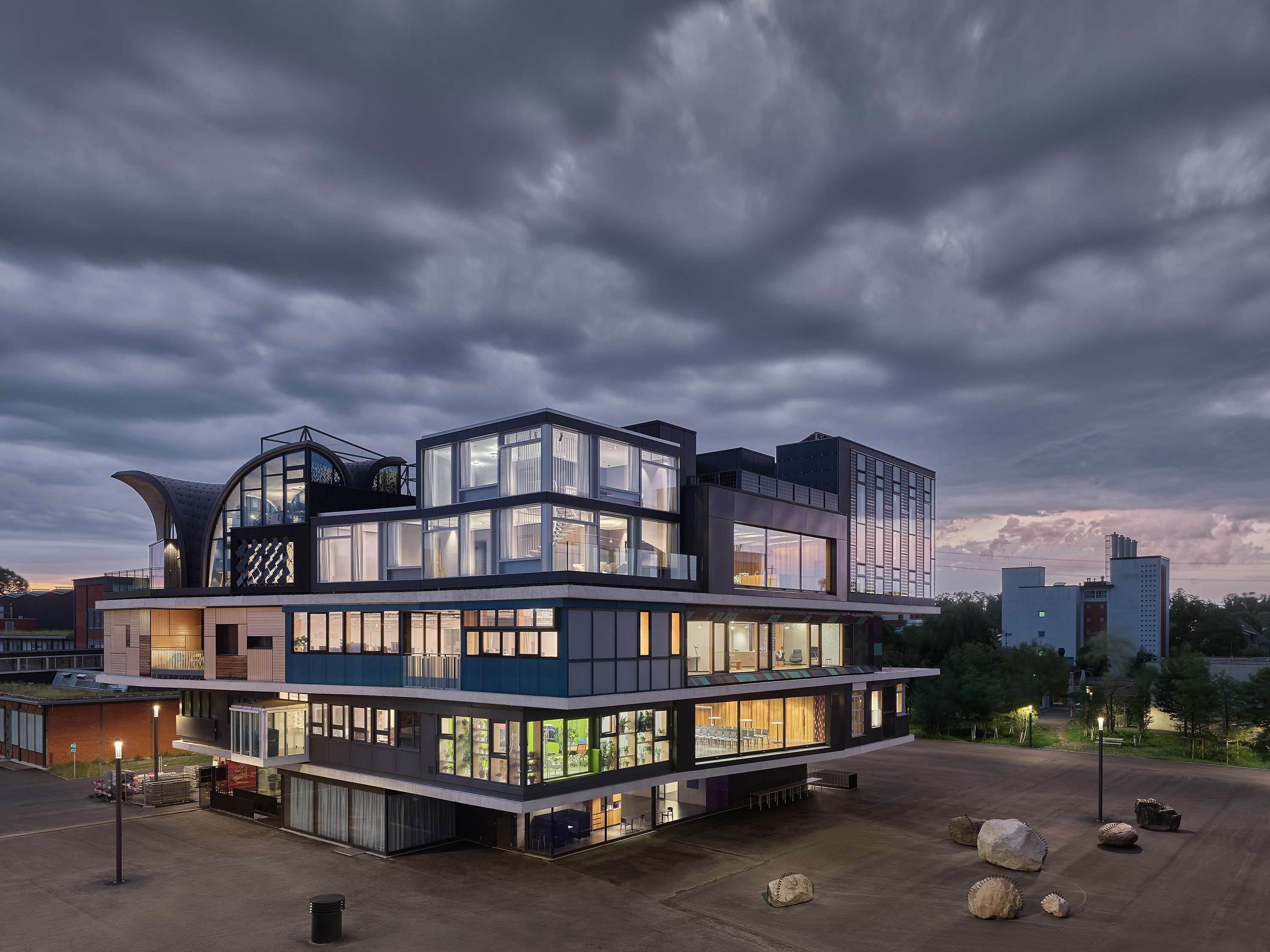
Project Information
Credits
Client
BASF Schweiz AG, Empa
Architecture
ROK Architekten
Selected partners
Aepli Metallbau AG, Stahlton Bauteile AG, Digital Building Technologies - ETH Zurich, BASF SE, Walt+Galmarini AG, re-fer AG, NDC - New Digital Craft, Bartenbach GmbH
Team
Michael Knauss, Silvan Oesterle, Fabio Amicarelli, Thomas Doleschel, Miguel Sumpsi Sanchez
Consultants
EBP Schweiz AG, Thomas Lüem Partner AG
Photography
Zooey Braun Fotografie, Andrei Jipa